Manutenção na Praça de Máquinas
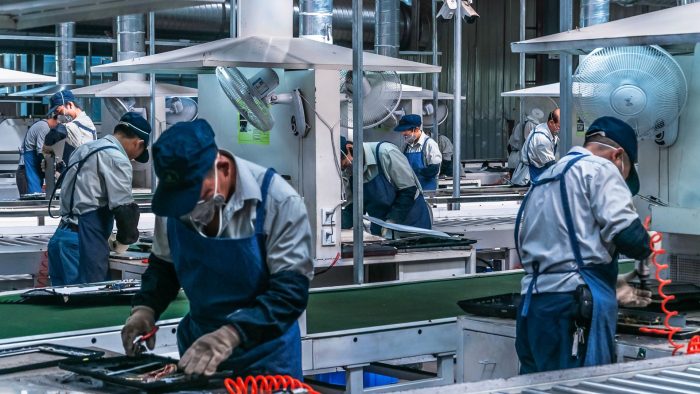
A palavra manutenção tem a origem do latim “manus tenere” , que significa “manter o que se tem”…
Manutenção Mecânica Industrial – Conceitos Básicos e Tecnologia Aplicada – Paulo Samuel de Almeida
Na vastidão dos oceanos, onde a operação segura e eficiente das embarcações é uma prioridade, a manutenção desempenha um papel crucial para manter o maquinário funcionando como projetado. No entanto, o conceito de manutenção vai muito além de simplesmente consertar equipamentos danificados; ele começa desde a fase de projeto, onde engenheiros se esforçam para facilitar manutenções preventivas e corretivas futuras.
A tecnologia evoluiu nas complexidades na montagem, desmontagem e na gestão da manutenção, originando 4 tipos:
- Corretiva
- Preditiva
- Preventiva
- Manutenção Centrada na Confiabilidade
Manutenção Corretiva
A manutenção corretiva ocorre após uma quebra ou parada inesperada do equipamento ou processo. Nesses casos, é necessária uma sequência de processos para restabelecer o funcionamento adequado.
Por exemplo, imagine um sistema hidrofórico com duas bombas em paralelo, sendo uma principal e a outra de backup. Verifica-se um vazamento na bomba principal pela carcaça, o maquinista deve verificar a causa do problema e proceder com a intervenção necessária, como a troca da carcaça ou soldagem, para retornar à operacionalidade.
A manutenção corretiva é evitada ao máximo, pois ocorre de forma imprevista e pode causar transtornos e impactos na segurança.
Manutenção Preventiva.
A preventiva é aquela encontrada nos manuais dos equipamentos e no sistema de manutenção da embarcação, são as manutenções planejadas, seja por tempo e/ou por hora de funcionamento.
O projetista avalia o desgaste do equipamento ao longo do tempo, e com base em diversas normas e critérios, elenca intervalos para inspeção e troca de elementos para manter o maquinário em funcionamento como no projeto.
Entretanto, muitas destas trocas ocorrem antes dos intervalos seja por erro do próprio projeto, má utilização do equipamento e últimas manutenções feitas fora dos procedimentos do fabricante.
Exemplo: O rolamento do motor elétrico do soprador utilizado na Unidade de Tratamento Séptico, dependendo do projeto deve ser trocado a cada 5 anos, entretanto para esses 5 anos serem seguidos, esse soprador deve estar em um ambiente com umidade e temperatura ideais para evitar um desgaste prematuro do rolamento, e assim, necessitando uma corretiva ou uma redução no intervalo na troca.
Essa manutenção traz vantagens como no planejamento logístico para os sobressalentes e planejamento de pessoal para fazer o serviço.
Manutenção Preditiva
Um diferencial na gestão de manutenção do navio, esse tipo de manutenção consegue avaliar a condição real do equipamento e cria uma tendência. Em outras palavras, utiliza-se instrumentos para medição de fenômenos físicos, seja temperatura, pressão, vibração, ruído e assim é possível fazer um diagnóstico do equipamento.
Exemplo: Um motor principal de propulsão tem seu óleo lubrificante purificado por um equipamento centrífugo, devido ao mal funcionamento desta centrífuga, o óleo não estava mais sendo purificado e estava tendo adição de água no óleo, devido a manutenção preditiva do maquinista, fazendo analise de água no óleo, foi constatado semanalmente um aumento de 0,1% na concentração de água. Logo antes do OIL MIST do motor alarmar e gerar um shutdown do equipamento em operação gerando transtornos e talvez acidentes , a equipe de máquinas diagnosticou o problema futuro e resolveu antes de gerar uma consequência grave.
Manutenção Centrada na Confiabilidade
Ela visa eliminar e prevenir defeitos, eliminando suas causas, essa manutenção é uma metodologia que segue 7 passos:
Seleção do sistema e coleta de informações: Identifica e documenta o processo e/ou sistema a ser analisado.
Análise de modos de falha e efeitos: São identificadas as falhas e seus modos e os efeitos causados por elas, utiliza a metodologia FMEA (Failure Mode and Effect Analysis).
Seleção de funções significantes: Utiliza os dados obtidos no passo anterior e determina se uma falha tem efeito significativo, considerando a segurança, meio ambiente, operação e economia do processo.
Seleção das atividades aplicáveis: Determina tarefas de manutenção preventiva que sejam tecnicamente aplicáveis para prevenir, corrigir ou amenizar cada modo de falha.
Avaliação da efetividade das atividades: constitui-se em um processo estruturado para determinar se uma tarefa de manutenção preventiva é efetiva para reduzir as consequências previstas para uma falha
Seleção das tarefas aplicáveis e efetivas: nessa etapa, utiliza-se um processo estruturado para determinar a melhor tarefa baseada em resultados do processo, impactos operacionais, segurança e impactos ambientais.
Definição da periodicidade das atividades: nessa etapa, estabelecem-se os métodos e critérios para definição da periodicidade ou frequência de execução das atividades selecionadas, assim como o planejamento e a estruturação do processo de implantação da metodologia os quatro subprocessos: Análise de Confiabilidade, Análise de Mantenabilidade, Análise de Produtividade e Otimização (SIQUEIRA, 2012)
Exemplo: O sistema DP da embarcação, é sempre realizada a manutenção centrada na confiabilidade. 1) Seleção do sistema e coleta de informações: Sistema DP e os equipamentos envolvidos. 2) Análise de modos de falha e efeitos: Utiliza a metodologia FMEA (Failure Mode and Effect Analysis), analisando as falhas de sensores e simulação de alarmes, no sistema de propulsão, geração, refrigeração e etc. 3) Seleção de funções significantes: É categorizada a gravidade de cada falha, umas gerando a perda do equipamento gerando uma perda significativa em manter a posição da embarcação, outros somente para indicar o operador a utilização de um equipamento em redundância, sem gerar perda de posição no curto prazo e etc. 4) Seleção das atividades aplicáveis: Criação de planos de manutenções focadas no sistema DP e a embarcação, baseada em normas e legislação, para amenizar os impactos ou eliminar as consequências das falhas. 5) Avaliação da efetividade das atividades: Avalia as manutenções preventivas, por exemplo teste de alarmes, para prevenção das falhas. 6) Seleção das tarefas aplicáveis e efetivas: Cria procedimentos de operação baseado em histórico ou planejamento prévio que gerem efeitos efetivos, exemplo um azimutal ligado em 2 barramentos e quando ocorre o blackout parcial de um dos lados, existe procedimento para restabelecimento por outro lado. 7) Definição da periodicidade das atividades: Baseado em histórico ou planejamento prévio cria periodicidade nas atividades de manutenção, teste, reavaliação e etc, sendo este passo com normas e legislação sobre o tema.
Mas, afinal sabemos o que é cada manutenção, como fazemos ser eficientes a bordo ?
É um trabalho em conjunto normalmente com o Chefe de Máquinas, Logísticas, Gerente da Embarcação, Pessoal de Projetos. Normalmente eles criam um plano de manutenção e melhoram o processo, e cada empresa tem o seu, entretanto existem procedimentos comuns entre todos.
Utilizam KPI para metrificar o processo, vou falar no detalhe:
Os KPIs (Key Performance Indicators), ou Indicadores-Chave de Desempenho, são uma parte fundamental do plano de manutenção para rodar o navio de forma eficiente. Eles são métricas quantificáveis e objetivas que auxiliam na avaliação do desempenho da manutenção, permitindo que a equipe de máquinas e náutica, e pssoal de terra, acompanhe o cumprimento dos objetivos estabelecidos.
Integrar KPIs em um plano de manutenção é essencial para garantir que as atividades de manutenção estejam alinhadas com as metas estratégicas da empresa e ajudem a otimizar a confiabilidade, disponibilidade e desempenho geral dos ativos da embarcação. Algumas das principais razões pelas quais os KPIs são importantes no plano de manutenção são:
- Medição do Desempenho: Os KPIs fornecem uma maneira clara e mensurável de avaliar o desempenho da manutenção. Eles ajudam a identificar áreas de melhoria, detectar tendências e monitorar o progresso ao longo do tempo.
- Identificação de Problemas Precocemente: Certos KPIs, como aqueles relacionados à manutenção preditiva, podem ajudar a detectar problemas em estágios iniciais, antes que se tornem falhas críticas.
- Gestão de Custos: Os KPIs podem fornecer informações sobre os custos de manutenção e ajudar a otimizar os gastos para garantir a eficiência financeira.
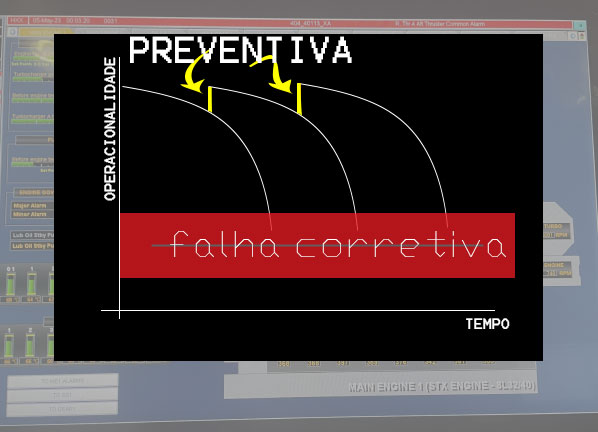
Alguns exemplos de KPIs relevantes para o plano de manutenção em uma embarcação podem incluir:
- Tempo Médio entre Falhas (MTBF): Mede o tempo médio decorrido entre duas falhas sucessivas de um ativo. Quanto maior o MTBF, maior a confiabilidade do ativo.
- Tempo Médio para Reparo (MTTR): Mede o tempo médio necessário para reparar um ativo após uma falha. Um MTTR mais curto indica uma resposta mais rápida da equipe de manutenção.
- Taxa de Confiabilidade: Representa a proporção de tempo que um ativo está disponível para operação. Uma alta taxa de confiabilidade é um indicativo de bom desempenho da manutenção.
- Índice de Cumprimento do Plano de Manutenção: Mede a proporção de tarefas de manutenção executadas conforme o planejado. Uma alta taxa de cumprimento indica uma execução adequada do plano.
- Custos de Manutenção por Unidade de Produção: Avalia os custos de manutenção em relação à produção gerada. Um custo menor por unidade de produção pode indicar maior eficiência.
Ao implementar um plano de manutenção bem estruturado com KPIs adequados, a empresa marítima pode garantir que seus ativos operem de forma confiável e eficiente, reduzindo o risco de paradas não programadas, aumentando a vida útil dos equipamentos e maximizando o retorno sobre o investimento em manutenção.
Mas, já adianto é muito complexo e difícil.
Existem problemas sérios na coleta de dados, na confiabilidade dos dados, no tratamento e na tomada de decisão. Meu sonho ….e é algo que a indústria vai ter que evoluir, é todos os oficiais, gerentes de embarcações dominarem ferramentas de BI, sem isso, não vamos alcançar a excelência. Um desafio para todos nós.
Comments
Very interesting info!Perfect just what I was searching for!Money from blog
Very interesting info!Perfect just what I was searching
for!Blog monry